Traitement sur aluminium
Conversion chimique
Alodine 1200 & Alodine 1500
La chromatation est un traitement de conversion chimique à base de chrome hexavalent. Les couches d’oxyde complexe obtenues sont de l’ordre du micron d’épaisseur avec un poids de couche d’environ 1 g/m² et de faible résistivité. La couche formée est une excellent base d’accrochage pour les finitions organiques et présente une bonne tenue à la corrosion. L’aspect est incolore pour une Alodine 1500 et va du jaune clair irisé à un brun marron clair pour une Alodine 1200. Pour l’alodine 1200 une couche jaune clair irisée caractérise un faible poids de couche (donc une faible tenue corrosion), une faible résistivité (donc une très bonne continuité électrique de la couche) ainsi qu’une très bonne base d’accrochage. A contrario, une couche brun marron clair caractérise un fort poids de couche (donc une très bonne tenue corrosion), une certaine résistivité (donc une moindre continuité électrique de la couche) mais présente une moins bonne interface de liaison pour les finitions organiques.
Surtec 650 & Lanthane 613.3
L’utilisation du chrome hexavalent dans les traitements de surface tend à disparaitre. Les nouvelles règlementations ont entrainé le développement de nouveaux procédés de conversion chimique. Nous utilisons depuis de nombreuses années le SURTEC 650 et le LANTHANE 613.3 qui sont des procédés à base de chrome trivalent et répond à la directive RoHS. D’aspect incolore à bleu irisé, ces traitements présentent les mêmes caractéristiques qu’une couche de conversion chimique habituelle. La tenue corrosion est cependant moins bonne qu’avec une Alodine 1200 (surtout pour les série 2000) et la très légère coloration de la couche ne facilite pas le contrôle des pièces lors de leur intégration.
ANODISATION
OAC
L’anodisation chromique est un traitement utilisé en industrie aéronautique pour ses propriétés anti-corrosion intrinsèques, son aptitude à l’adhérence des finitions organiques (peinture, collage structurel avec composite, etc..), son influence modérée sur les caractéristiques de fatigue, sa très faible influence dimensionnelle (pour des pièces avec tolérances très sérrées) et sa particularité à révéler la structure métallurgique de l’alliage d’aluminium (grain, fibrage, hétérogénéité liée au traitement thermique, etc…). De plus, en cas de rétention de produit lors du traitement de pièces mécanosoudées ou de fonderie ou de géométries complexes, elle ne présente aucun risque d’attaque du métal de base contrairement à l’anodisation sulfurique. Ce sont des couches d’oxyde qui présentent un meilleur coeficient de frottement que celles obtenues en OAS mais ont une moins bonne résistance à l’abrasion. Les couches sont d’aspect opaque plus ou moins foncées en fonction de l’alliage et d’une épaisseur de l’ordre de 2 à 8 µm. La microdureté superficielle de celles-ci est de 200 à 250 Hv0,05. Leur tension de claquage est de 300 à 600 volts et la tenue corrosion va d’environ 100h pour une couche non colmatée à 350/500 h pour un colmatage eau chaude avec additif jusqu’à 750 h et plus pour une couche colmatée au bichromate de potassium. Ce sont des couches qui peuvent être colorées noires. La couche d’oxyde qui se forme lors de ce traitement de conversion électrochimique se traduit comme pour l’OAS par 1/3 de son épaisseur en croissance et 2/3 en pénétration dans l’alliage de base.
OAD
L’anodisation dure est une forme particulière d’oxydation en bain d’acide sulfurique. Car ce procédé est mis en oeuvre dans un bain à très basse température (-5°C) ce qui autorise l’application de fortes densités de courant (2,5 à 4 A/dm²), minimise la dissolution de l’oxyde formé et permet donc d’atteindre des épaisseurs beaucoup plus importantes qu’en OAS (30 à 80 µm). L’oxyde ainsi obtenue présente une structure très dense conférant à la couche une très grande dureté, une très bonne résistance à l’abrasion ainsi qu’un fort isolement électrique et thermique. La couche peut être uniquement colorée en noire car la coloration intrinsèque de l’alliage d’aluminium au cours du traitement d’anodisation dure va du bronze clair ou gris souris à un brun sombre ou gris anthracite en fonction des composés métalliques de l’alliage (voir photo ci-contre en sortie de rinçage après OAD). L’épaisseur de couche se forme pour moitié en pénétration dans le métal de base et pour moitié en croissance. Etant données les épaisseurs de couches importantes que l’on peut obtenir, il faut prendre en compte ce phénomène de gonflement et procéder à une décote à l’usinage des pièces avant traitement. Pour une épaisseur de 50 µm de couche on obtient une microdureté superficielle de l’ordre de 300 à 500 Hv0,05 (fonction de l’alliage). La tension de claquage résultante est de 500 à 1000 volts et la tenue corrosion va d’environ 50h pour une couche non colmatée à 250/300 h pour un colmatage eau chaude avec additif jusqu’à 500 h et plus pour une couche colmatée au bichromate de potassium.
OAS
En application des normes : MIL-A 8625F type II, NF A 91450, EN 2284 Traitement de conversion électro-chimique mis en oeuvre dans un bain d’acide sulfurique en solution acqueuse et à une température de 18 à 22 °C. La pièce qui est reliée à l’anode d’un redresseur de courant subit une densité de courant défini (1,2 à 1,5 A/dm²) durant 20 à 60 minutes produisant une couche d’oxyde poreux de 5 à 25 µm ayant une microdureté superficielle de 100 à 300 Hv0,05. En pratique ce traitement s’effectue à tension constante de 10 à 20 voir 25 Volt. Cette couche d’oxydation peut éventuellement être colorée (or, rouge, bleu, gris, vert, etc…) et/ou colmatée. Ces couches présentent un isolement électrique de 500 à 1000 volts et leur tenue à la corrosion va de 100h sans colmatage à 300 h avec colmatage à chaud plus additif et plus de 500 h si colmatée avec des sels de chrome. L’épaisseur de ces couches varie de 5 à 10 µm dans le cas d’une OAS dite « de décoration » et de 10 à 25 µm pour une OAS dite « de protection » ( ou mécanique).
Dans le cas de l’anodisation de décoration :
- Il s’agit de former une légère couche anodique décorative, qui bien que conservant l’aspect de surface de la pièce, permettra sa coloration et améliorera « la durée de vie relative » à l’usage (résistance à la rayure, tenue à la corrosion en milieu peu agressif). Les couches obtenues restent donc les plus transparentes possibles, de l’ordre de 5 à 10 µm.
Dans le cas de l’anodisation de protection :
- Il s’agit de former une couche anodique protectrice, pouvant être colorée et avec une très bonne tenue d’aspect dans le temps (résistance à la corrosion). Son objectif est d’améliorer les caractéristiques mécaniques de la surface de la pièce traitée. Les couches obtenues, de l’ordre de 10 à 25 µm, sont plus résistantes à l’usure et ont des propriétés d’isolation électrique.
TSA
Le TSA, Anodisation Sulfo-Tartrique a pour objectif de remplacer l’OAC, Oxydation Anodique Chromique.
L’anodisation dure est une forme particulière d’oxydation en bain d’acide sulfurique. Car ce procédé est mis en oeuvre dans un bain à très basse température (-5°C) ce qui autorise l’application de fortes densités de courant (2,5 à 4 A/dm²), minimise la dissolution de l’oxyde formé et permet donc d’atteindre des épaisseurs beaucoup plus importantes qu’en OAS (30 à 80 µm). L’oxyde ainsi obtenue présente une structure très dense conférant à la couche une très grande dureté, une très bonne résistance à l’abrasion ainsi qu’un fort isolement électrique et thermique. La couche peut être uniquement colorée en noire car la coloration intrinsèque de l’alliage d’aluminium au cours du traitement d’anodisation dure va du bronze clair ou gris souris à un brun sombre ou gris anthracite en fonction des composés métalliques de l’alliage (voir photo ci-contre en sortie de rinçage après OAD). L’épaisseur de couche se forme pour moitié en pénétration dans le métal de base et pour moitié en croissance.
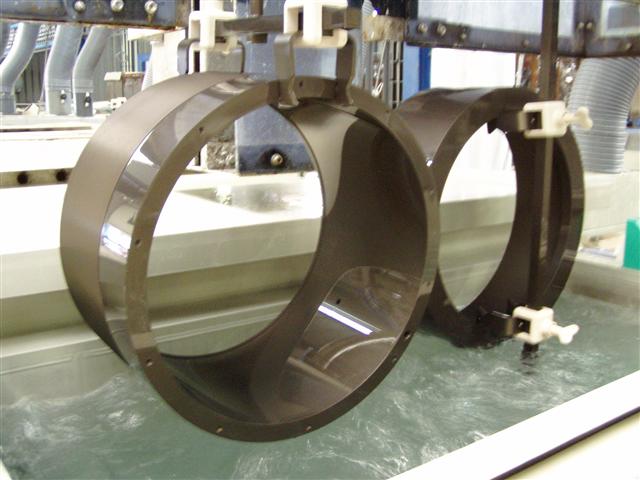